.Desarrollo estratégico para PYMES
Por Graciela Medrano
Licenciada en Logística. Especialista en Calidad. Owner – Fractal Consultora Logística
Una compañía que quiere permanecer y ser competente en el mercado debe saber que el desarrollo de estrategias de crecimiento no sólo está direccionado a mejorar las ventas, sino también a diferenciarse frente a la competencia ofreciendo experiencias de valor.
Las estrategias de crecimiento se pueden dar a través de una expansión interna o externa. La elección dependerá de diferentes factores, tales como la etapa del ciclo de vida del negocio, la saturación del mercado, la necesidad de un rápido crecimiento, el nivel de recursos, etcétera.
Si el crecimiento es interno éste se llevará a cabo mediante la creación de nuevos establecimientos, centros de distribución, nuevas plantas productivas, nuevas oficinas, controlando estrictamente la expansión y asegurándose de que toda la compañía cumple los objetivos. Este desarrollo facilita la optimización de las localizaciones y de la distribución. Los recursos crecen paulatinamente, por lo que la financiación del mismo es más accesible además de permitir la adquisición de tecnología de punta. Algunas pequeñas o medianas empresas dan un salto cuantitativo entre poseer un depósito de materias primas o artículos para la venta a desarrollar un centro de distribución y logística propio. Para los expertos en Logística; el diseño de un centro de distribución muchas veces es tarea compartida entre arquitectos, ingenieros y contadores por lo que el cálculo de las dimensiones y necesidades requiere de un trabajo en equipo interdisciplinario.
Relevamiento previo al diseño.
Para el cálculo de las dimensiones y lay out de un centro de distribución se debería realizar un relevamiento de necesidades teniendo en cuenta los perfiles descriptos a continuación.
· Perfil de disponibilidad del área: se refiere al espacio físico con el que se cuenta. Es necesario conocer el espacio en m2, edificabilidad permitida, límites y aspectos geográficos como el terreno y los riesgos de inundación. También es necesario conocer las zonas reservadas como oficinas, zonas de parking, zonas verdes u otras que por aspectos legales no puedan ser usadas.
· Perfil de inventario: se define en función de la política de inventario y el perfil de productos, distinguiendo las cantidades a almacenar por familia de artículos. Se calculan necesidades volumétricas que se validan contra el histórico y se corrobora que estén alineadas con la estrategia de abastecimiento y políticas comerciales. Tener en cuenta un espacio para productos descontinuados, en proceso, en cuarentena, etc., que pueden llegar a ocupar entre un 15-20% de la capacidad de almacenamiento. Otro factor a considerar es la estimación de la densidad medida en picos de almacenamiento y el vaciamiento operativo.
Los módulos de almacenamiento y tipos de estantería adecuadas son un factor clave en el cálculo de la capacidad de almacenamiento, productividad en movimientos y layout del centro de distribución.
Perfil termométrico: si una porción de los SKU a almacenar y distribuir tienen distintas temperaturas de conservación y manipulación; habrá que proyectar una cámara y/o central de frío o congelados con áreas definidas de acopio, picking y preparación de pedidos y con temperatura controlada acorde a las necesidades. Para el cálculo de estas zonas de acopio y preparación especiales hay que analizar los SKU afectados y realizar la proyección de expansión y crecimiento para dicha línea de productos con el mismo encuadre que para los SKU de
temperatura ambiente. Se tendrán en cuenta los materiales y equipos necesarios para manipular mercadería en estas zonas de temperaturas diferentes a la ambiente como así también los requerimientos de Salud y Seguridad Ocupacional del personal afectado a dichas tareas.
- Perfil de acopio: es la estimación del flujo y movimiento de artículos desde las posiciones de almacenamiento hacia las ubicaciones de despacho, y es función de la cantidad y tipos de pedido. Se obtiene al medir las cantidades de pedido para separarlas según la ventana de tiempo de preparación y el flujo de despacho de vehículos. Se pueden considerar diferentes tipos por ejemplo, por orden de salida, por camiones, para obtener el flujo de unidades (cajas, pallets, litros, etc.) que se deben movilizar, combinando la cantidad de entrega y almacenamiento de los diferentes productos.
- Perfil de despacho: es necesario para identificar el número y tipo de vehículos que se cargarán con pedidos; se definirá en función de la demanda y las ventanas de entrega a los diferentes tipos de clientes y destinos.
La capacidad de despacho debe incluir la holgura para atender variaciones de demanda en la ventana de tiempo de preparación. No se debe calcular sólo con el promedio por que sería insuficiente, ni puede estar establecida como el máximo observado, porque se generaría exceso de recursos.
· Perfil de recepción: abarca el flujo y movimiento de artículos desde las puertas y muelles de recepción hasta las ubicaciones de almacenamiento. Puede contemplar recepción de materias primas, productos en proceso, áreas de cuarentena, tránsitos aduaneros, devoluciones, etc. Así como en el perfil de despacho las estimaciones se hacen en número de vehículos, el perfil de recepción incluye la estimación de movimientos (cajas, pallets, bidones, granel) que se necesitan almacenar y el tiempo y tipos de muelles necesarios.
Es conveniente definir áreas para staging al final de cada proceso; las mismas son zonas destinadas a almacenar por períodos cortos lo que se ha procesado en una etapa de una operación en espera a que pase a la siguiente. Por ejemplo, entre recepción y almacenaje se deja el producto recibido a controlar.
· Perfil de proyecciones: el layout no se calcula esperando cumplir las necesidades actuales sino las futuras. Por esto, se deben considerar proyecciones a futuro separadas para almacenamiento, recepción, despacho y recolección. Es recomendable proyectar con, al menos, cinco años como horizonte de planeación e identificar los picos operacionales para minimizar el riesgo de disminución de la operación, el impacto de tener una obra civil en medio de los procesos en curso y en el caso de las expansiones, una alteración de las operaciones.
Consideraciones del layout: el diseño debe considerar la distribución espacial como así también el flujo de productos y espacios adecuados para circulación y maniobra de equipos. La selección del layout definitivo se basa en criterios de productividad, costos, inversión, cualitativos y de operaciones.
Otras áreas a considerar: habitualmente en el layout no se tiene en cuenta las áreas administrativas. Se recomienda considerar baños, vestuarios, lockers, oficinas de operación (sala de reuniones, capacitación, comedor) y archivo, cuarto de máquinas, entre otros. También son necesarias otras zonas operacionales como: zonas de devoluciones y roturas, pallets vacíos, parqueo de autoelevadores y sala de carga de baterías, área para el mantenimiento de equipos, material de embalaje, sala de espera de conductores, zona de residuos. También se debe tener en cuenta iluminación, características de los pisos (planicidad, cargas, juntas), redes eléctricas, algún acueducto, etc. Aquí solo se hace referencia a los aspectos logísticos, los cuales son frecuentemente olvidados.
· Perfil de equipos: hay distintos equipos que se pueden comprar o alquilar para ser usados en un centro de distribución, los cuales van a depender de la configuración definida. La solución al equipamiento puede variar debido al tamaño y peso de los SKU a manejar, la altura definida en el diseño del centro de distribución, el ancho de pasillo, su confiabilidad y la disponibilidad del proveedor para suministro y mantenimiento. Si la clasificación de SKU lo requiere y si la opción manual de cargas pesadas es elevada y repetitiva se puede considerar la instalación de elevadores de carga por vacío para levantar bolsas pesadas, tambores, cubos, cajas de cartón y bultos de manera eficiente con cabezales intercambiables para múltiples aplicaciones.
Necesidad de un balance de carga de la operación: dicho balance tiene su origen en el análisis de las necesidades de recursos versus los requerimientos de flujo de movimientos. Tener menos equipos resta eficiencia y afecta la productividad, incurriendo en un menor servicio. Por otro lado, tener equipos de más genera sobrecostos.
· Perfil tecnológico: la información permite la eficiencia y rastreo de los flujos físicos a controlar. Todas las zonas que comprenden el centro de distribución deben estar perfectamente identificadas. Una codificación sencilla, por colores o carteles, podría funcionar bien para un bajo número de SKU. Sin embargo, si el número de referencias y flujo de producto es muy alto se recomienda el uso de WMS (Sistema de Gestión de Almacenes). La importancia de estas soluciones informáticas es que permiten manejar consistentemente la información de manera que se optimizan los flujos de recepción, almacenamiento, despacho y reabastecimiento.
Perfil de equipos tecnológicos: la tecnología RFID es una de las opciones tecnológicas disponibles en el mercado que permite optimizar la recepción de mercancías, siendo éste uno de los procesos empresariales más arduos de automatizar. Los datos de los SKU que ingresan, que son heterogéneos en su naturaleza y en su packaging, son imprescindibles para la trazabilidad a través de toda la cadena. Con la automatización y simplificación de este proceso empresarial se puede obtener un buen control y registro de ingresos, captura de datos claves, eliminación de operaciones improductivas, alertas de validación, etc.
Otros sistemas tecnológicos que optimizan espacio y tiempo son los sistemas automáticos de almacenamiento y preparación de pedidos que mejoran tiempos de picking, bajan los costos operativos y reducen la capacidad de almacenamiento pero tiene una inversión inicial elevada por lo que hay que considerarlos en una etapa secundaria.
Diseño y desarrollo sustentable.
La sustentabilidad desde el marco ambiental tiene como objetivo minimizar o evitar el consumo de recursos no renovables, en el ámbito social debe generar diseño orientado a las personas que fomente la interacción y finalmente no debe dejar de ser rentable.
Si el diseño del centro de distribución es sustentable desde el inicio, mediante la optimización del uso de recursos como el agua y la energía, la minimización de residuos y la búsqueda de mejorar las condiciones ambientales, el desarrollo tiene un marco que le agrega valor y no se aleja de la rentabilidad.
Ejemplos:
Construir el centro de distribución con materiales de manufactura local o regional, de baja reflexión de calor para exteriores y techos.
Gestionar el manejo de aguas pluviales mediante reservorios y sistemas de canales que se extiendan por los terrenos aledaños para garantizar la integridad de los mismos.
Reducir el uso de energía eléctrica utilizando fotocélulas y sensores de movimiento para la optimización del circuito de iluminación.
Alimentar los artefactos eléctricos como termotanques y motores con energía generada por paneles solares.
Reducir el uso de agua potable mediante la implementación de griferías de caudal reducido con doble descarga y sistemas automáticos.
Reciclar los pallets una vez desechados por terceros.
Separar los residuos en origen para su tratamiento.
Colocar vegetación circundante para que opere como una barrera de absorción al dióxido de carbono.
Instalar extractores para ventilar el ambiente de trabajo logrando una renovación de aire adecuada. La puesta en marcha de edificaciones eficientes y respetuosas del Medio Ambiente garantiza la sustentabilidad de la empresa y minimiza el impacto en su entorno.
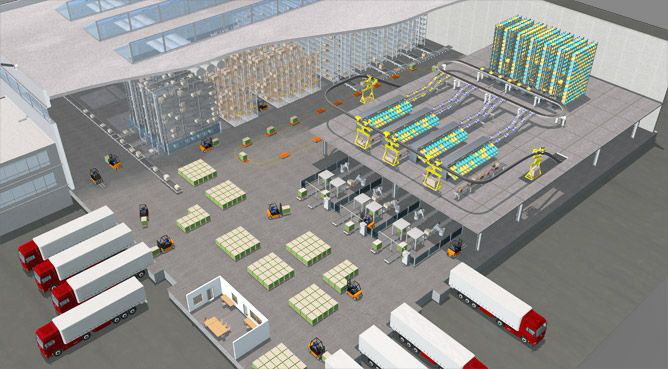
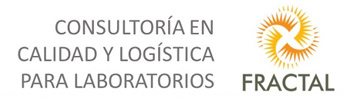